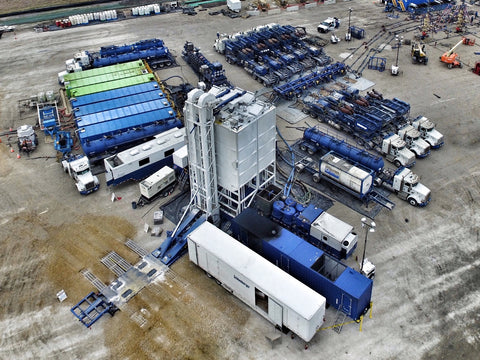
Failure Prediction for High Pressure Pumping Equipment
Failure Prediction for High Pressure Pumping Equipment
The Problem:
The rise in US domestic oil production over the last decade has been driven primarily by advancements in hydraulic fracturing technology. Hydraulic fracturing operations treat wells with specialty fluids pumped at extremely high pressures and flow rates, often in excess of 2,500 gallons per minute at over 15,000 psi. The specialty fluids are also often a carrier fluid for a proppant, usually course sand. The resulting fluid properties and conditions are highly erosive to the valves on the dozen or more high pressure pumps required by these operations, and this erosion results in very frequent maintenance operations. Repairing these high pressure pumps requires multiple skilled personnel, and an ill-timed pump failure can delay a fracking operation, resulting in non-productive time for millions of dollars worth of equipment, and dozens of skilled operators.
The Data:
Our client, a hydraulic fracturing service provider, collects and stores sensor data from all their pumps, as well as associated fluid properties, and maintenance records. This data is monitored and stored in a mobile operations control unit, where the supervisors and engineers oversee the operations.
The Solution:
Hydraulic fracturing operations are performed in stages, each lasting several hours with down time in between. We used the historical sensor data, conflated with the maintenance logs, to predict when a failure was likely to occur in an upcoming frack stage, before that stage had begun. The deployed model provided alerts to the supervisors and engineers at the wellsite when a given pump was likely to fail during the next one or two stages, and allowed them to schedule preventative maintenance during the down time between stages.
The Impact:
By turning a reactive maintenance event into a proactive maintenance event, this model was able to reduce the non-productive time due to these failures, without increasing the overall cost of maintenance on the pump units. When deployed fleet-wide, our client realized a total annual savings of over $1 million.