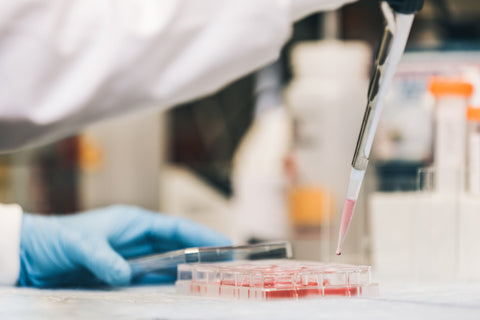
Predictive Lab Testing to Streamline QAQC Procedures
Predictive Lab Testing to Streamline QAQC Procedures
The Problem:
The construction process for oil & gas wells includes periodically placing cement between a steel casing and the open hole. This cement sheath is a primary barrier for ensuring well integrity, preventing ground water contamination, and preventing blow outs. The cement blend needs various additives to provide the correct fluid properties for a given set of well conditions, which can often exceed 300°F and 10,000 psi. Due to variations in well conditions, design requirements, material lots, and water chemistry, each cement blend needs to be customized. The process of designing these custom cement blends is called pilot testing. It is an iterative process in which a lab technician chooses a reference blend from a similar well and runs a series of time consuming tests, adjusting the chemical additives whenever a test results are out of spec. A typical cement blend can require dozens of testing iterations to refine, and can cost over $2,000 on average in overhead and utilization for the technicians and testing equipment.
The Data:
Our client, a global cementing service provider, maintained an internal software tool to assist lab technicians with the design process, including a database of cement blend designs and test results. Two types of tests require the most iteration in design: rheology, controlled primarily by the type and concentration of a dispersant, and thickening time, controlled mainly by the type and concentration of chemical retarder.
The Solution:
We applied our machine learning toolbox to create models which predicted the results of each lab test from a given cement blend design. We then deployed the models as a module in the lab design software. A user then input their proposed design, and received the predicted test results. This allowed them to digitally simulate as many designs as needed before running the physical tests.
The Impact:
After model deployment, the client's cement labs saw over a 50% reduction in lab tests per design. This translated to over $1,000 in savings per design. This project had the additional effect of reducing drilling rig non-productive time due to delayed lab testing, and also allowed each lab to support services to more drilling rigs concurrently.